认 证:工商信息已核实
访问量:138255
盐城紫光建材设备有限公司. 0000-00-00 点击2218次
前言 矿渣是炼钢过程中排出的工业废料,经水急冷处理后成为粒状颗粒。它具有结晶相及玻璃相二重性的性质,因此矿渣的活性既取决于析出晶体种类及晶体的数量,又决定于玻璃态数量及性能。矿渣中含有较多的钙成分,在形成过程中生成了一些硅酸盐、铝酸盐及大量的玻璃质,其化学成分与硅酸盐水泥熟料成分相接近,主要是CaO、SiO2、AL2O3、MgO、FeO等氧化物和C2S、CAS2、C2AS、C3A、C2F和CaSO4等硫化物,具有独立的水硬性,在氧化钙与硫酸钙的激发作用下,遇到水就能硬化,通过细磨后,能使其硬化过程大大缩短。 矿渣微粉具有的潜在水硬性,使其掺入混凝土不仅可以等量取代水泥,而且可使混凝土的多项性能得到极大改善:泌水少,可塑性好;水化析热速度慢,水化热小,有利于防止大体积混凝土因内部温升引起的开裂;矿渣微粉内的钙矾石微晶可补偿因混凝土中细粉过多引起的收缩;硬化混凝土具有良好的抗硫酸盐、抗氯盐、抗碱-活性集料反应性能,并能使后期强度得以大幅度提高,具有良好的耐久性。 大量的试验研究表明:用作水泥混合材的矿渣,当细度达到350m2/kg以上时,才具有增大掺量、保持水泥性能的作用;而要成倍提高掺量或大幅度改善水泥强度,粉磨比表面积则需达到450-600m2/kg。然而,这种细度对于矿渣具有相当大的粉磨难度,一是因为矿渣颗粒由连续网络状结构的玻璃体组成,粉磨要打破这种结构十分困难;二是矿渣的粉磨特性又决定了粉磨产品中能起比表面积主导作用的0-5um的粒级含量偏少,因而粉磨要获得高比表面积并非易事。正因为如此,传统的粉磨方式由于不能达到足够的细度而抑制了其活性的充分发挥,故生产中仍仅作一般混合材使用,尤其是矿渣硅酸盐水泥的最大掺量普遍只在25%左右,尚不足国标允许最大值(70%)的一半。显然寻求矿渣有效的超细粉磨工艺,对改善水泥及其制品性能,节省熟料,降低生产成本,以及资源的综合利用等方面,目前的生产现状都存在较大的挖掘潜力。 目前通常采用熟料和混合材分别计量同时粉磨的工艺技术路线。运用这种工艺生产的矿渣水泥通常在水泥性能上表现为:水泥的早期强度偏低,后期强度偏高;生产上表现为:矿渣掺量不能大幅度提高,或提高矿渣掺量而管磨机产量降低,电耗剧增。其主要原因是由于矿渣和硅酸盐水泥熟料的易磨性有较大的差异,在相同粉磨工况下,熟料较易磨细,矿渣则相对偏粗,成品中<10um的含量少。当矿渣掺量较少时,其影响不明显,当掺量较大时,产品比表面积则因难以达到足够的细度而必然以降低产量为代价来保证水泥的性能。显然,传统的粉磨工艺既要想达到不降低管磨机产量又能多掺矿渣的目的是不现实的。 针对矿渣的难磨特性,国内许多水泥厂进行了多种粉磨工艺的实践,分别粉磨即是其一(见图一)。 这一工艺根据熟料、矿渣两种物料的不同粉磨特性,采用两台开流管磨机分别进行粉磨,是提高矿渣掺入量的有效途径。分别粉磨既可按需求的细度控制矿渣比表面积,也可使熟料的粉磨因难磨组分的减少而更易于控制水泥细度和提高产品的性能。 1目前管磨机生产矿渣微粉工艺现状 1.1开流管磨机系统 该系统与开流水泥粉磨系统基本相同。其特点是:①对入磨矿渣水分控制要求高,需配烘干系统;②工艺流程简单,操作方便,设备运转率高,投资低;③产量低,系统综合电耗高。 1.2管磨机加选粉机组成的圈流系统 该系统和圈流水泥粉磨系统相同。其特点是:①对入磨矿渣水分控制要求高,需配烘干系统;②工艺流程较复杂;③系统综合电耗比开流系统低;④产量比开流系统要高,同时技术管理要求及投资也略高。 1.3传统粉磨方式的不足 上述两种工艺都是采用传统的管磨机作为粉磨核心设备。传统管磨机粉磨效率不高,究其原因是在粉磨过程中,一方面,管磨机内的物料虽然在沿着管磨机从磨头到磨尾的纵长方向上的细度是由粗到细,直至出磨为合格料,似乎形成了一个合理的细度梯度。但从沿纵向的每一个点的横截面来看,物料的粒度粗细悬殊,极不均匀,有的还很大。这些粗大的颗粒一旦进入研磨仓,要磨至合格的细度,需要更多的时间,这是因为研磨仓的主要功能是对细粉的研磨,破碎能力很微小。另一方面,在磨内沿着管磨机纵向的粉磨物料逐步细化,有些早期较细的粉料过早地成了合格粉料,却不能及时的排出磨外。对于开流磨来说,因少量的粗颗粒过早与细物料一起混入研磨仓,而耗费大量的研磨时间,使合格物料不能及时排出磨外,而消耗大量的能量。非要等到全部粉磨物料达到合格后,才能排出磨外。对于圈流磨来说也同样存在粗细颗粒差异大,物料不能在合理的粉磨机理下作业的问题。 同时上述两种矿渣微粉生产系统都是按常规水泥生产设备及工艺粉磨矿渣的,而不是使用符合矿渣粉磨特征及矿渣微粉要求的粉磨设备及工艺,因此,存在着电耗高、生产成本高的不足,影响了效益的发挥。 2 管磨机生产矿渣微粉工艺 针对传统矿渣粉磨的不足,我公司提出的管磨机生产矿渣微粉工艺。它具有投资省、电耗低的特点。既适合老系统的改造,又适合新建的矿渣粉磨系统。 2.1矿渣粉磨特征及产品要求 矿渣具有粒度小、脆性大、易破碎、难研磨的特点。因其含有较多的结晶相及玻璃相,其结构为连续网络状,不存在应力集中的界面,粉磨就是要打断这种玻璃体中的Si-O键,难度很大,且矿渣粉要求比表面积高。《用于水泥中的粒化高炉矿渣技术标准》中规定“大于10mm颗粒含量(以重量计)合格品不大于8%,优等品不大于3%”,而平均粒径仅2-3mm。所以应尽一切可能调整管磨机的破碎能力,增加其研磨能力。 2.2 管磨机生产矿渣微粉工艺 管磨机生产矿渣微粉工艺分为:开流系统矿渣微粉生产工艺和圈流系统矿渣微粉生产工艺。 2.2.1 开流系统矿渣微粉生产工艺特点 紫光 管磨机开流系统矿渣微粉生产工艺是在普通管磨机的基础上,以紫光公司A型筛分装置为核心,通过合理设置仓数、仓长、衬板和研磨体,合理调节管磨机的破碎、研磨能力,实现提高矿渣微粉质量、增产降耗的目的。 ●管磨机仓数及仓长比 和国内其它公司技术不同,紫光公司管磨机矿渣微粉生产工艺中的管磨机一般分为两仓磨:一仓为细碎仓,二仓为研磨仓。保证矿渣在一仓得到充分细碎的同时,尽可能的调整二仓的长度,以延长矿渣在二仓的研磨时间。 ●研磨体及其级配 采用管磨机开流系统矿渣微粉生产工艺,管磨机的细碎仓研磨体一般采用钢球、大钢段。具体要视入磨矿渣的粒度、水分、管磨机的衬板结构特点等来选择合适的研磨体,以保证细碎仓的破碎兼粗磨的功能实现。相同情况下,在细碎仓用钢棒作为研磨体比钢段好,主要是钢棒的冲击力大、棒隙小,对粉磨的矿渣有选择性,故粉碎速度快。在管磨机的研磨仓中采用微段或微球作为研磨体,通过增加研磨体表面积的方式,达到提高研磨能力的目的。 ●A型筛分装置 A型筛分装置(另有文献介绍)是实现研磨仓的微型研磨体发挥最大研磨能力的基础。运用A型筛分装置最大的好处是:可以控制不同范围的粒径物料在不同的工作区接受破碎或研磨,使其在最合理的研磨机理下完成粉磨作业,提高粉磨效率。但选择适合的A型筛分装置应根据管磨机的规格、矿渣在细碎仓的细度、矿渣的水分、产量、质量的要求来确定。 ●管磨机衬板的确定 矿渣粉磨系统在管磨机功率、研磨体形式、装载量、级配等确定后,对管磨机的衬板进行重新设计显得非常重要。传统的衬板(如阶梯、大波纹、小波纹等)是根据水泥熟料的易磨性、水泥成品质量要求来设计的,用于矿渣粉磨应有所改变。在细碎仓,如果采用常规形式的阶梯衬板,研磨体由于提升高度过高,则使研磨体无法抛落到矿渣聚集的部位,影响粗磨能力,同时阶梯衬板同向安装交接处存在死角,也影响到矿渣的细碎和粗磨。如果采用小波纹衬板会由于提升能力不足,造成对破碎能力的影响。因此,在细碎仓需采用重新设计的提升能力介于阶梯衬板和小波纹衬板之间的双波纹衬板较合适。 在研磨仓,为了提高微段或微球的研磨效率,必须加大衬板的带微段或微球的能力,增加微段或微球的动能和运动范围。因此采用重新设计的加高波纹高度的研磨仓专用衬板三波纹衬板或环沟形衬板较为合适。同时为了克服因研磨仓加长,研磨体小可能导致的研磨体运动中的“涡流”现象,应采用高效的“反螺旋活化衬板”和溢流挡料环,安装后在磨内形成错落有致的布置方式,让研磨体在不同空间层面上受到激活充分发挥其研磨功能,同时改善距离筒体衬板较远的研磨体的运动强度,激活物料的抛撒区,使冲击、剪切、研磨等多种粉磨机理在磨内合理搭配,从而实现粉磨效率的提高。 ●A型出料装置 提高研磨仓的研磨能力,一方面提高研磨体的研磨面积和增加研磨体的动能,另一方面延长矿渣在研磨仓内的停留时间,控制料段(球)比,加大研磨机会来提高研磨能力。普通管磨机的出料篦板,不仅不能实现上述功能,而且由于研磨仓采用微段(球),很容易出现堵塞现象。采用具有料段(球)分离功能的强溢流型A型出料装置,不仅实现料微段(球)分离,而且可以达到延长矿渣在研磨时间,增加料段(球)比,提高产品比表面积的目的。 综上所述,采用A型管磨机开流系统矿渣微粉生产工艺,管磨机除了磨机筒体,磨头衬板外,磨内所需配件都需重新进行设计和改进,才能真正实现高产低耗生产矿渣微粉的目的。 3.2.2 管磨机圈流系统矿渣微粉生产工艺的特点 采用管磨机圈流生产矿渣微粉工艺时,不仅可以生产高比表面积的成品,而且相比开流系统而言,能获得较高的产量,电耗更低。管磨机的改造内容基本和开流生产矿渣微粉工艺相同,只是改造中的结构参数和一些工作参数不同,这里不再多述。实际上采用圈流系统生产矿渣微粉时,管磨机只是解决磨得出的问题,即获得较高粉磨效率。而选得出是选粉机和成品收尘器所要解决的问题,选粉机的选粉效率和成品收集效果会对矿渣粉磨系统有着重要的影响。 ●ZGX高效细粉选粉机 矿渣单独粉磨时通常要求有较高的比表面积,一般希望在350m2/kg以上,进入选粉机的物料平均粒径只有10~12μm左右,最大的粒径也只有50~60μm左右,而且矿渣的密度远小于水泥的密度。目前用于水泥生料和水泥熟料粉磨系统上的普通选粉机无论在撒料、分级和成品收集的性能方面,都无法满足矿渣粉磨系统的生产要求。选粉机对不同属性粉料的分级必须具有相应的“识别”性能,只有这样才能满足系统的生产要求。 目前国内用于矿渣磨的选粉机多是在O-Sepa选粉机基础上,改变选粉机的运行参数,在结构上没有作变化。主要措施是提高选粉机的主轴转速,从而获得微粉。因此选粉机的功率消耗变大,如目前配Ф3×11m管磨机粉磨矿渣微粉的选粉机主轴电机一般选配75kw。紫光公司紫光ZGX细粉选粉机根据矿渣微粉颗粒细,重度小,从其涡流场产生惯性离心力和气流的粘滞力对粉料的作用所形成的切割粒径的原理入手进行设计,使其不仅有很高的矿渣微粉“识别”能力,而且功率消耗很低,只是国前国内同类产品的40%左右。 下表为某厂Φ3.0*11m矿渣磨配ZGX1000选粉机生产比表面积430 m2/kg矿渣粉时的性能情况. 粒径(µm) <5 <10 <20 <30 <40 <50 <60 <80 <100 选粉机喂料含量(%) 7.8 18.2 38.7 58.4 68.5 75.4 92.1 98.9 100 选粉机粗料含量(%) 1.3 2.8 6.7 12.8 18.4 28.5 56.9 94.3 100 选粉机成品含量(%) 11.2 29.1 58.3 79.4 91.6 95.4 99.7 100 100 循环负荷(%) 130-150% 选粉效率(%) 80%左右 ●成品收集除尘器 采用圈流系统生产矿渣微粉时,选粉机的成品收集装置一般均采用气箱脉冲布袋除尘器。在生产过程中常常会发现系统的循环负荷并不高,但选粉机的选粉效率低的现象。绝大多数客户认为这是选粉机性能不行,其实成品收集除尘器的不足往往被忽略。由于矿渣的重度小,与水泥相比,在同样的料气比的情况下,矿渣粉的实际体积的粉料量增多了,含尘浓度高多了,相应的收尘效率和流通阻力也会发生改变。气箱脉冲布袋除尘器用于矿渣微粉收集时,其运行参数和结构需根据矿渣微粉的特性作相应的改动,否则会使收尘器整体运行阻力大。随着阻力的不断增加,高压离心风机的风量减少(这是由于高压离心风机的软特性造成的),这又造成选粉机的料气比过大,选粉机的性能下降,选粉效率降低。 气箱脉冲布袋除尘器阻力(进出口压差)由收尘器的本体、滤袋及吸附在滤袋上的粉尘等三部分组成。收尘器的本体(结构)阻力主要由进出风口、风道、各袋室进出风口、袋口等气体通过的部位产生的摩擦阻力和局部阻力有关,即为各部位摩擦阻力和局部阻力之和。 阻力的大小与气体流速大小的平方成正比。因此设计中应尽可能扩大气体通过的各部位的面积,最大限度地降低气流速度,减小设备本体阻力损失。依据这个原则,在富乐公司气箱脉冲袋除尘器技术基础上,我们设计出用于超细矿渣微粉收集用的系列气箱脉冲布袋除尘器,同时装备Bi-Get节能系统和Emc清袋系统。 依据多年的使用经验,大灰量且锁风要求较高的场合不宜采用分格轮,为此,我们设计了专用卸灰阀。该阀结构简单,卸灰量大,密封效果好,且不需动力驱动。 当确定好合适的过滤风速(气布比)后,设备结构的优化设计相当重要,不合理的结构设计会导致运行阻力升高,影响系统达产,增加电耗。有的用户在收尘器阻力高时,不得不提高清灰压力、加快清灰频率,这样做,不但没有降低设备的运行阻力,反而加快了滤袋的破损,增加了运行成本和检修工作量,因为设备结构阻力跟清灰没有关系。 3结束语 由于矿渣的物料特性和对矿渣粉的要求不同,应采用适宜矿渣粉磨的工艺系统,这样才能提高粉磨效率,同时也提高能量的利用率。使用管磨机生产矿渣微粉其工艺简单,操作方便,运转率高,产品颗粒级配合理,生产成本低。运用该技术对江苏某粉磨站Φ3.2*13m矿渣磨系统进行改造,选粉机和除尘器改造后,功率消耗从原来的299kw下降到220kw,系统产量从原来的24.6t/h提高到27.8t/h,吨矿渣微粉综合电耗从原来的71kwh/t下降到66kwh/t,每年仅节电就达40多万元。同时系统投资较辊式磨、辊压机、立式磨等矿渣微粉生产线系统可节省80-300%,是系统技术改造和投资的理想选择。 参考文献 1. 廖晓樱,《提高P·S水泥中矿渣混合材掺量的工艺途径》; 2.孔祥忠,《中国立窑水泥厂粉磨系统的技术改造任务》; 3.胡建鹏,矿渣微粉系统袋收粉器的设计,《中国水泥》 4. 朱启春, 《开流矿渣微粉管磨机特点及其应用》;
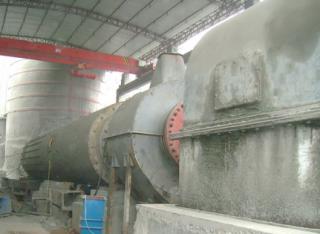